In the world of industrial machinery and electric motor development, there’s a quiet revolution happening—one driven by innovations in components like **hysteresis brakes**, **hysteresis dynamometers**, **hysteresis clutches**, and advanced **motor test systems**. These unsung heroes are the backbone of industries ranging from automotive manufacturing to renewable energy, ensuring that every motor spins with precision, efficiency, and reliability. Let’s dive into how these technologies are reshaping the future of testing and automation.
---
### The Magic of Hysteresis Technology: More Than Meets the Eye 🧲
At the heart of many motor testing systems lies **hysteresis technology**—a principle that leverages magnetic fields to control motion with unparalleled accuracy. Unlike mechanical systems that rely on friction, hysteresis devices use non-contact magnetic forces, eliminating wear and tear. This means longer lifespans, reduced maintenance, and consistent performance even under extreme conditions.
**Hysteresis brakes**, for example, are widely used in applications requiring smooth torque control. Imagine a robotic arm assembling delicate electronics or a conveyor belt adjusting speed seamlessly—these brakes provide the precise resistance needed without jerks or slippage. Similarly, **hysteresis clutches** enable controlled Smart web guide equipment in scenarios where gradual engagement is critical, such as in medical devices or aerospace mechanisms.
---
### Dynamometers: The Ultimate Motor Test Equipment 🚀
When it comes to validating motor performance, **dynamometers** are the gold standard. Among them, **hysteresis dynamometers** stand out for their ability to simulate real-world loads with exceptional fidelity. Whether testing an electric vehicle’s drivetrain or a wind turbine’s generator, these dynamometers measure torque, speed, and power output while replicating dynamic conditions like sudden accelerations or variable resistances.
Why does this matter? Consider the automotive industry. Engineers rely on motor dynamometers to ensure that EVs deliver optimal range and efficiency. By mimicking hills, stop-and-go traffic, or high-speed cruising, these systems help refine designs before a single prototype hits the road. The result? Torque VS current and motors that meet—or exceed—global standards.
---
### Motor Test Systems: Where Innovation Meets Integration 🔧
A single component rarely tells the whole story. Modern **motor test systems** combine hysteresis devices, sensors, and software to create end-to-end solutions. These systems don’t just collect data—they analyze it in real time, providing actionable insights for R\u0026D teams.
Take, for instance, a company developing drones. A comprehensive test system could evaluate a motor’s response to rapid throttle changes, temperature fluctuations, and vibration. By integrating hysteresis brakes to apply load and advanced software to model flight scenarios, engineers can identify weaknesses early, ensuring reliability when the drone is miles above the ground.
---
### Sustainability Through Smarter Testing 🌱
As industries push toward greener practices, motor test equipment plays a pivotal role. Efficient motors consume less energy, and precise testing ensures they operate at peak efficiency. Hysteresis-based systems contribute here by minimizing energy loss during testing. Traditional mechanical brakes dissipate energy as heat, but hysteresis dynamometers convert it into measurable data, reducing waste.
Consider a factory upgrading its HVAC systems. By using motor test systems to validate high-efficiency motors, the facility could cut energy consumption by 20% or more. Multiply this across thousands of installations, and the environmental impact becomes staggering.
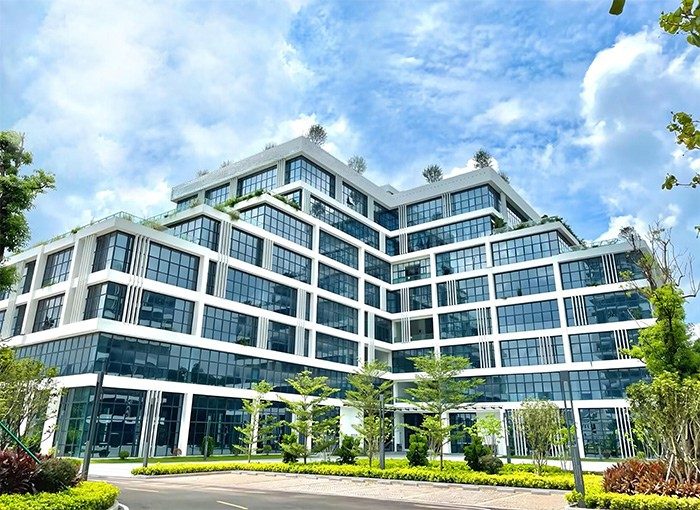
---
### Case Study: Elevating Electric Vehicle Performance ⚡
Let’s look at a real-world example. A leading EV manufacturer faced challenges with battery drain during regenerative braking. Their existing test setup couldn’t accurately replicate the interplay between the motor, battery, and braking system.
By integrating a hysteresis dynamometer into their motor test system, the team simulated hundreds of driving cycles, from steep descents to urban traffic. Motor dynamic performance tests ’s precise load control allowed them to fine-tune the regenerative braking algorithm, boosting energy recovery by 15%. This breakthrough not only extended the vehicle’s range but also reduced reliance on traditional friction brakes, lowering maintenance costs.
---
### The Future: AI, IoT, and the Next Generation of Testing 🌐
What’s next for motor test equipment? The answer lies in connectivity and intelligence. Imagine a hysteresis brake that adjusts its torque based on live data from a motor’s embedded sensors or a dynamometer that uses machine learning to predict failure modes before they occur.
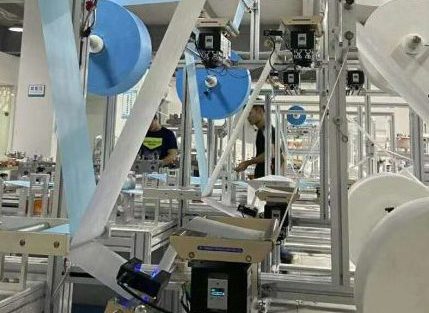
IoT-enabled Industrial control solutions are already making waves. Remote monitoring allows engineers in New York to oversee tests in Tokyo, while predictive maintenance algorithms notify technicians when a component nears its service limit. This isn’t science fiction—it’s the direction the industry is headed, and companies that adopt these technologies today will lead tomorrow.
---
### Choosing the Right Partner for Your Testing Needs 🤝
Not all motor test systems are created equal. When selecting equipment, consider factors like:
- **Accuracy**: Look for systems with sub-1% measurement uncertainty.
- **Flexibility**: Can the setup adapt to different motor types (AC/DC, servo, etc.)?
- **Scalability**: Will it grow with your needs, from prototype testing to full production?
- **Support**: Does the provider offer training, calibration, and troubleshooting?
A trusted supplier will tailor solutions to your specific challenges, whether you’re testing micro-motors for wearable devices or megawatt-scale generators.
---
### Final Thoughts: Why Precision Matters 🎯
In an era where margins for error are shrinking—whether in energy efficiency, safety, or performance—investing in advanced motor test equipment isn’t optional. Hysteresis brakes, dynamometers, and integrated test systems are the silent enablers of progress, turning theoretical designs into real-world marvels.
From the assembly line to the open road, these technologies ensure that every motor hums with purpose. And as industries evolve, so too will the tools that test them, driving us toward a future where precision isn’t just a goal—it’s a guarantee.
---
Emoji-free zone? Never heard of her. 😉 Whether you’re an engineer, a project manager, or a sustainability advocate, remember: the right test equipment doesn’t just measure performance—it defines it. Ready to power up your next project? Let’s talk torque.