In the ever-evolving landscape of industrial automation and motor-driven systems, the demand for reliable, accurate, and adaptable testing equipment has never been higher. From automotive engineering to renewable energy applications, the ability to validate motor performance under diverse conditions is a cornerstone of innovation. Enter hysteresis-based technologies—hysteresis brakes, dynamometers, and clutches—which have redefined the boundaries of precision and durability in motor testing ecosystems.
THE SCIENCE BEHIND HYSTERESIS TECHNOLOGY
At the core of these systems lies the principle of hysteresis, a phenomenon where magnetic materials exhibit lagged response to changes in applied magnetic fields. Unlike traditional friction-based systems, hysteresis devices operate without physical contact, eliminating wear and tear while delivering smooth torque control. This non-contact mechanism ensures consistent performance over extended periods, making hysteresis brakes and dynamometers ideal for applications requiring repetitive testing cycles.
HYSTERESIS BRAKES: THE UNSUNG HEROES OF LOAD SIMULATION
Hysteresis brakes excel in scenarios where precise load simulation is critical. Imagine an electric vehicle motor undergoing endurance testing: the brake must replicate real-world resistance, from uphill climbs to sudden deceleration. https://bluish-banana-zjxn65.mystrikingly.com/blog/revolutionizing-motor-testing-and-control-with-advanced-hysteresis-and with heat dissipation and wear, but hysteresis brakes maintain stability even at high RPMs. Their ability to adjust torque instantaneously via electronic control allows engineers to simulate dynamic conditions with microsecond-level accuracy.
CNC servo press applications include:
- Zero maintenance due to absence of friction components
- Silent operation, ideal for noise-sensitive environments
- Linear torque output independent of rotational speed
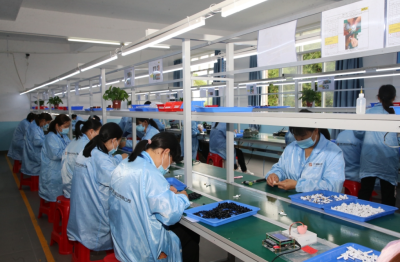
Applications span industries such as aerospace (testing drone propulsion systems) and consumer electronics (validating precision motors in medical devices).
HYSTERESIS DYNAMOMETERS: MEASURING PERFORMANCE, DEFINING EXCELLENCE
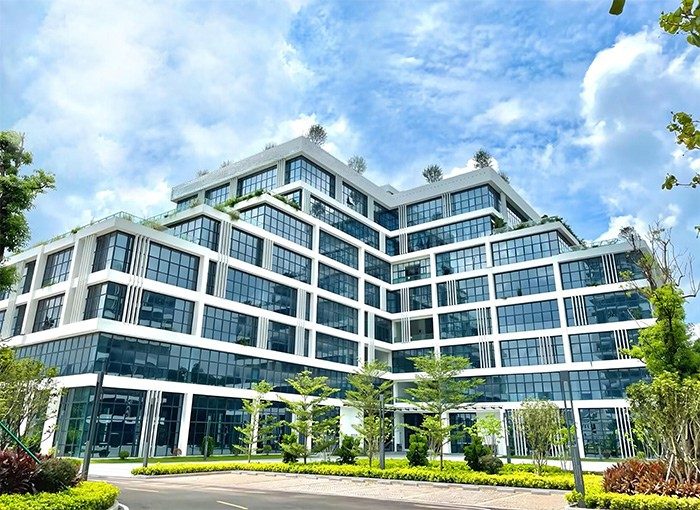
When quantifying a motor's power curve or efficiency metrics, hysteresis dynamometers offer unparalleled versatility. These systems measure torque and speed while applying programmable loads, enabling comprehensive performance mapping. For instance, a wind turbine generator test might involve simulating gusting winds and sudden load drops—conditions easily replicated by hysteresis dynamometers through software interfaces.
Electric motor testing systems over eddy current or hydraulic counterparts include:
- Broader speed ranges (from near-zero to ultra-high RPM)
- Minimal inertia, allowing rapid load changes
- Compatibility with regenerative energy recovery systems
Automotive manufacturers leverage these dynamometers for benchmarking EV drivetrains, where subtle variations in efficiency translate directly into competitive range advantages.
MOTOR TEST SYSTEMS: WHERE COMPONENTS BECOME SOLUTIONS
A modern motor test system integrates hysteresis devices with advanced instrumentation, creating a holistic testing environment. Consider a robotics company developing servo motors for assembly lines: the test system must validate not just torque and speed, but also response times under varying voltages and temperatures.
Critical subsystems in such setups include:
1. Hysteresis clutches for simulating inertial loads
2. Multi-axis torque sensors for 3D force analysis
3. Thermal chambers mimicking extreme operating conditions
4. AI-driven analytics platforms predicting failure modes
These systems empower R\u0026D teams to compress months of field testing into weeks of lab simulations, dramatically accelerating time-to-market.
HYSTERESIS CLUTCHES: PRECISION IN MOTION CONTROL
Often overshadowed by their brake and dynamometer siblings, hysteresis clutches play a vital role in applications requiring slip-controlled torque transmission. In conveyor systems for pharmaceutical packaging, these clutches ensure delicate products aren't crushed by sudden jolts. By magnetically regulating Aviation components without physical contact, they achieve smooth engagement that mechanical clutches can't match.
Emerging applications include:
- Precision tension control in semiconductor wafer handling
- Shock absorption in robotic joint mechanisms
- Energy-efficient HVAC damper control
INNOVATION IN MOTOR TEST EQUIPMENT: BEYOND BASIC VALIDATION
The latest generation of motor test equipment transcends simple pass/fail criteria. Advanced systems now incorporate:
- Real-time digital twins comparing physical motors with virtual prototypes
- ISO 17025-compliant calibration suites for regulatory adherence
- IoT connectivity enabling remote monitoring across global facilities
A case in point: An industrial pump manufacturer reduced warranty claims by 40% after implementing test systems that simulate abrasive fluid dynamics using hysteresis-based load banks.
Custom CNC servo press systems THROUGH ADVANCED TESTING
As industries push toward net-zero goals, hysteresis technologies contribute significantly to energy efficiency. Regenerative dynamometers can feed up to 90% of absorbed power back into the grid during testing—a game-changer for high-volume motor production facilities. Moreover, the durability of hysteresis components reduces electronic waste compared to traditional systems requiring frequent part replacements.
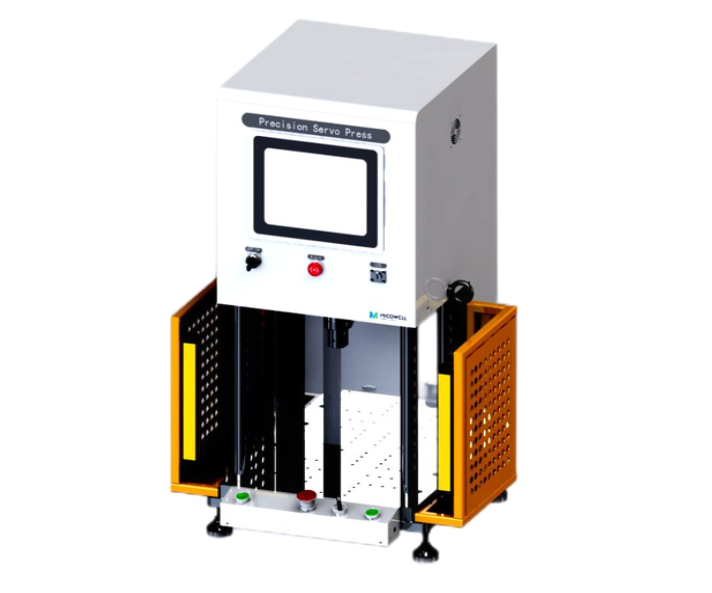
FUTURE HORIZONS: AI AND HYSTERESIS SYNERGY
The integration of machine learning with hysteresis-based test systems is unlocking new frontiers. Adaptive algorithms now automatically adjust test parameters based on real-time performance data, identifying subtle anomalies invisible to human operators. In one breakthrough application, an AI-enhanced system detected bearing wear in electric motors 300 hours before failure—preventing costly production line shutdowns.
CONCLUSION: THE MEASURE OF PROGRESS
In a world where motor efficiency differences of 0.5% separate market leaders from followers, hysteresis-based testing solutions provide the resolution needed to innovate with confidence. Whether optimizing e-mobility platforms or perfecting micro-motors for wearable tech, these technologies form the invisible backbone of quality assurance.
For engineers specifying test equipment, the choice transcends hardware—it's about selecting partners who understand that every decimal in a torque curve represents months of R\u0026D effort. Hysteresis systems, with their blend of physics-based reliability and digital-age adaptability, continue to set the standard for what rigorous testing means in the 21st century.
As industries confront challenges from electrification to smart manufacturing, one truth remains constant: You cannot improve what you cannot measure. With hysteresis-driven motor test systems, the art of measurement becomes a catalyst for transformation—transforming ideas into innovations, and innovations into revolutions.